Reference: Retrofit riveting- and welding machine
As the first retrofit project of eaw Relaistechnik GmbH, an automatic riveting- and welding machine from our own machinery was to be completely modernized. The aim of this first retrofit project was, on the one hand, the complete modernization of the plant, and on the other hand, the development and validation of know-how in order to meet the technical and economic requirements of such projects to be able to do so.
Eike Kammer, Projektleiter Retrofit
+49 (0) 3375 2131-155
E.Kammer@eaw-relaistechnik.de
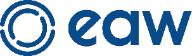
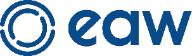
Problem Statement
As the heart of relay production, the plant has been producing contact springs for EAW's mechanical relays since 1975. A circulating tool chain guides spring plates along various Processing stations every three seconds. Rivet switch pieces are fed and riveted to the spring plates and a contact knife is welded onto them. Finally, the finished contact springs are bent and sorted.
Of course, decades of operation have not left the plant unscathed. In the course of time, the quality deteriorated noticeably, downtimes became more frequent and spare parts were no longer available in many cases.
The outdated welding technology could hardly be adjusted, so that new materials could not be processed satisfactorily. Furthermore, the process had become so unstable that constant intervention was necessary and the plant operators were completely blocked during production.
However, the main motivation for acting here was the incalculable risk of an irreparable failure of the control technology and the fact that the system no longer met the current requirements for functional safety.
Performance
Mechanics & Surface Preparation
Despite a long list of problems, the solid mechanics of the system were in good condition, which allowed various components to continue to be used. The system was completely dismantled and every component was analyzed, evaluated and refurbished. Surfaces were cleaned and powder-coated, and damaged components were remanufactured.
Electrical Engineering and Automation Engineering
The antiquated URSALOG 4000 controller has been replaced by a current Siemens controller + HMI. As a control concept, a state machine based on the OMAC PackML was implemented, which is not only suitable for packaging machines. By using the new automation technology, all relevant process and production data can now be recorded, visualized and offered for further processing via an I4.0-compliant interface (OPC UA).
The error-prone cam derailleur for detecting the chain position has been replaced by a precise absolute encoder, which provides decisive advantages for process monitoring. The mixing of different sensors that has developed over time has been replaced by the use of standard components, which guarantees a certain degree of manufacturer independence in the procurement of spare parts.
The outdated phase angle welding system was replaced by high-performance medium-frequency technology. The possibility of precise monitoring and control of the welding processes enabled a significant increase in welding quality and process stability. Another advantage of the new welding technology is that the system operators no longer must carry out parameterization themselves, but simply select the desired product type and start the production process.
In addition to the entire electrical equipment, the pneumatics were also renewed and brought up to date. The use of modern and efficient components significantly reduces the energy consumption of the system and leads to significantly improved maintainability in all areas.
Risk Assessment & Technical Documentation
Due to its age, the plant does not have a CE marking. In many cases, the requirements in force at the time of construction also no longer corresponded to those currently in force. On this basis, a risk assessment had to be carried out and the plant upgraded in accordance with the applicable guidelines, including the creation of complete and legally compliant technical documentation. The documentation of the electrical and fluid power was carried out using E-Plan P8, while technical drawings were created using Solid Edge. As a result, the CE conformity could be verified and we assume manufacturer responsibility without hesitation.
Results at a glance
As a result, the customer, in this case our own production, was able to hand over a practically new system. Finally, the concrete results of this retrofit project will be emphasized once again.
- Optically and mechanically completely overhauled system
- New electrical equipment and automation technology
- New Fluid Technology
- Complete and legally compliant technical documentation
- Successful Risk Assessment & CE Certification, Long-term spare parts supply
- I4.0-compliant interface for integration into SCADA or ERP system
- More than 50% space savings compared to the "old system" (integration of control and welding technology into the machine table)
- Energy savings during operation thanks to efficient pneumatics and welding technology
- Significant increase in the quality of the products to be manufactured